CHS 2010.2 had a public release in the middle of January. So approximately six weeks have passed where customer have been able to get their hands on this fresh juicy ripe piece of software and install it and admire it. People like myself could get advance builds of the release and prod and poke around, er, sorry diligently work through serious customer use cases. There’s always something new in CHS it seems, new is almost commonplace.
Without boring you about the difference CHS developers understand between functions and features (suffice it to say features are bigger) there are fifty new substantial things which have come into the software. And if you are not satisfied with that, then how about the two brand new products? One of the new products is Capital Modular XC, bringing into the Capital Harness XC application suite advanced capabilities for the KSK/Base-Overlay/Parent-Child/Build-to-Order techniques to handle complex multi-part designs. Sorry there are so many different ways to name-check this way of designing and building wire harnesses, I had to include most of the popular ones so nobody reas this and just thinks: “Huh?”
Users of CapH Classic have been using a similar capability in Europe in that product, so this is something of a re-write rather than a brand-new development, and I must say from my perspective having used both now, out with the old and in with the new as my preference.
However, the pick of the new features for me is something in Capital integrator. When you are designing using a topological integration, this phase becomes the fulcrum, and the data assembled, analyzed, validated and processed can become overwhelming. Side-whelming too. From both sides in these days of dozens of ECU’s per vehicle, and thousands of customer choice variations to satisfy the marketplace.
Of the sprinkling of improvements which came into the Capital Integrator product I especially commend to customers the Integrator Assistant feature. Let’s say you are designing the wiring for a car with about 2,500 wires. That’s approximate, because the real total will depending on what is in the vehicle model, and which one of say eighty instrument panel harnesses connects with which one of sixty body harnesses. in summary, more deluge of data than an engineer (and these are very smart engineers who work on this part of a design) can handle. The design assistant feature provides a configurable single point of reference for design diagnostic information. Wire routing and synthesis can within this single point of reference be previewed, signal route states can be viewed . It is quicker and simpler than before to troubleshoot for problems.
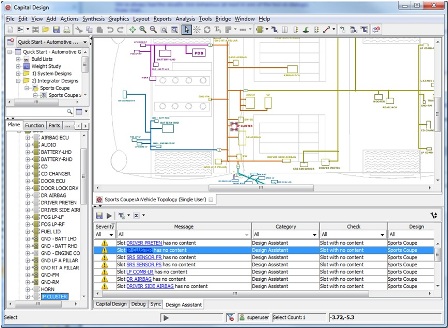
It is helpful to have the right information presented in one location, and in just the right quantity.
Too much information and you can end up ignoring pertinent information. Too little information and engineers waste cycles chasing spooks instead of being guided to the source of issues. I think Capital Integrator is striking the right balance with this way of doing things. Wasn’t poor before by any means, but the requests of customers for additional help has had the effect of improving the software. Thanks.