This is the concluding section of a short series of looking ahead to the new decade of harness engineering and electrical systems design for automotive and other transportation sectors. This final post is dedicated mainly to a short assessment of the physical implementation of the designs – the raw materials and sub-assemblies. My personal opinion is either correct or incorrect. Time will tell and although it may be interesting to look back in five or ten years and see how much I missed the mark or what unexpected new things surfaced My purpose is to start you on the path of considering the same issues – what will be same and what will be different over the next ten years. With a concept of what’s going to be static and what is likely to change I strongly advise you devise your own plans.
Series finale lesson is to reach for an ideal. It is good to aim to mold the circumstances of your working life rather than have the circumstances molding you.
The first decade of the 21st century just finished may be when the complexity of wiring harnesses reached a peak. However I will not bet “all-in” that this will be the case. In a well established industrial activity and a modern pattern of materials usage plus a large economic footprint you have to say a royal flush of inertia beats two pairs of techies with boundless enthusiasm for new ways of working any time.
That may be a great ring terminal you have there made of zirconiz-plastiform-greenstuff. Add on to the research and development costs the $3 million re-tooling expense for harness assembly. Hmm. There’s a lot of inertia. Price tags like that inject a fair amount of conservatism into the debate.
-
Predictions of drastic reductions in copper content in automobiles have consistently been wrong over the last 20 years. Multiplexing, flat-flexible cable and fiber optic technologies have had their advocates and seen implementations but not had widespread adoption in the market. Twisted circuits in cars for CAN/LIN and other in-vehicle networks have not yet reached a peak. Expect them to top out in about 3 years as functions become integrated on a single processor unit, single storage in new cars.
- The growing use of Electronic Control Units has not resulted in an overall decrease in the numbers of wires or the weight of copper used in a vehicle. Extended use of networks to route signals through vehicles will suppress an increase in total number of wires, but will still leave designers with considerable challenges in managing the resulting complexity. The number of user choices offered has a multiplier effect on the number of harness build-able levels. Interest in the techniques to address the burden of managing the data will focus on feature-based algorithms and modular-composite design techniques for mass market passenger vehicles. Tools which give visibility and control to the engineers earlier in working out the complexity implications of design and additional feature choices will become indispensable.
- Societal, consumer and legislative pressure to use recyclable materials and improve fuel efficiency is going to increase over the next decade. I’m not a genius that can predict the spikes and troughs of copper prices over the next 10 years, but my amateur research is enough to give a forecast prices will at some stage over the decade be double what they are now. Might stay that way. Copper alloy wires containing less copper per linear length than stranded copper wire will become common. Copper clad aluminum wires for example are suitable for many applications which currently use conventional stranded copper wires.
- I expect connector and terminal systems to slowly evolve. Lighter, more durable parts will take a toehold in the market. What works in wiring harnesses however is immediate cost reduction – so if you have something cheaper than the currently used connector system to pitch to the OEM then you have a shot at displacing the connector system which has been virtually unchanged for 40 years or more. Manufacturers will invest R&D effort into validating and updating terminal systems for the copper alloy types of wire and competitive advantage will come from a tight international distribution system.
- In the next 10 years I do not forecast a drastic move away from labor intensive assembly for wiring harnesses. Many manual manufacturing operations are inherently difficult to replace with automation in harness assembly and where it is possible take considerable capital investment to do so. Neither harness makers nor their customers have have a long event horizon making it easy to show such investment’s returns. Therefore the price cutting war shows no sign of stopping soon and assembly workers in Chile for example will be the competition for their Argentinian brothers and sisters in the industry. Process automation robots are not invading and taking over the shop floor any time soon.
Vehicles are mobile computing platforms – information and entertainment platforms stacked with communications equipment. Liberally sprinkled with data gathering devices and sensors, electronically processed real-time and near-real time. Not just passenger cars – trucks and airplanes, trains and agricultural and off-road vehicles rely on these systems. Paradoxically this has only increased the logistical challenges of the OEM – for whom software/firmware updates are now a headache to control. Nevertheless the complexity of the electrical interconnect systems shows no sign of reducing. Managing user selectable options, the aggregation and disaggregation of electrical content from composite designs, validating designs as legitimate and consistent with upstream and downstream needs, working out manufacturing combinations and levels and identifying trade-offs and give-aways is still a terribly complex affair.
Some things will definitely not change. Nice people will continue to finish last.
-
Those electrical engineers will be consuming the data after the mechanical model is nearly but not wholly complete.
-
The wiring manufacturing engineers will take harness data late from the design engineers.
-
Customers will hand off data to suppliers late and incomplete and flawed.
-
Librarians will be notified at the eleventh hour of component symbols and sub-component relationships which need to be added or maintained for a project.
-
Customer-led and component sourcing decisions will necessitate tear-up of designs at the last minute regardless of what the project timing plan says about freezing. Engineers will be responsible for making things work.
It is nice of these people to do their work last. Until the mechanical engineers design their work around a vehicle’s electrical systems this will continue to happen. Until the customer is not right all the time this will prevail.
How about those all-electric cars? Well, the decade 1910 to 1920 was when electrically powered cars became uneconomic to produce competing against mass produced internal combustion engine vehicles. Ten decades later there’s a chance of a come-back.
Those nice people the electrical engineers may have the last word.
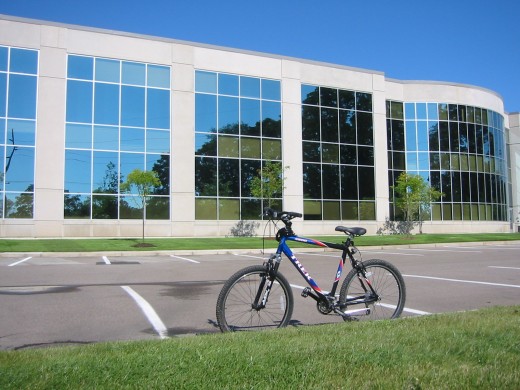
An example of transportation without a wiring harness - Mentor Graphics Detroit office in background